Agate Making Process
Raw materials used in agate bead making are found in the rich geological deposits of Baluchistan and Gujarat. The deposits of Gujarat are particularly important because of the high saturation of iron minerals in the agates, which upon heating produces a deep red-orange carnelian. Mining in Gujarat is controlled by state contractors who usually hire labors from the local Bhil tribal communities. During the dry seasons of the pre- and post-monsoon, men, women and children, using simple tools, mine the agates by digging tunnels into the Miocene agate conglomerates of the Babaguru Formation (Gadekar 1978). The nodules are collected at loading points or stockpiled in local villages where the contractors sell them to middlemen or merchants from Khambhat.
At various stages during the mining, sorting and stockpiling, flakes are struck from the nodules to determine the quality of the agate. This selection process results in discrete scatters of cortex flakes and rejected nodules that are distinguishable archaeologically and could be used to document important activity areas.
The manufacturing process of agate includes steps such as sun drying, breaking larger stones into small sizes, slicing of the stones, rounding in a ball mill, shaping on grinding wheels, polishing, drilling holes, and assembling the final product. All of the mentioned steps are carried out by different sets of workers as for example, fodia (chipper) or ghasiya (polisher) etc. Primary size reduction job is done by chippers
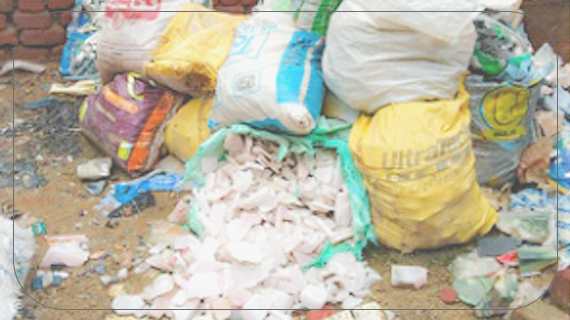
Drying
After the nodules are brought to Khambhat they are dried in the sun to remove the moisture that is trapped inside the rock. This manufacturing stage is usually carried out for two to three months beginning in March, and large stockpiles of drying nodules are located next to the habitation or workshop of the merchant where they can be easily monitored. Special quality raw materials are laid out to dry on rooftops or enclosed courtyards where no pilferage is possible.
In the context of large-scale production, considerable quantities of lower quality and some potentially good quality raw nodules become scattered and lost in drains, or Embedded in the soil of the courtyard or alley way, and particularly along the edges of the unpaved streets.
When the nodules have been thoroughly sun dried they are baked in teracotta vessels or simple pit kilns to remove any remaining moisture, making the rock more homogeneous and easier to flake.
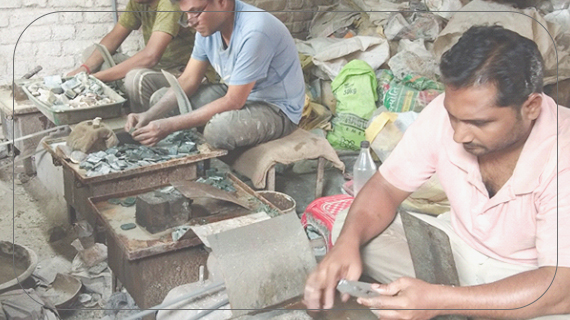
Stone cutting
Bigger size agate stones are cut by the machines which are Installed at only few places. Assigned artisans are only engaged in this process who does only the cutting part. So, the other artisans get their cutting work done by them and then proceed with their other work. These machines produce lot of noise and dust.
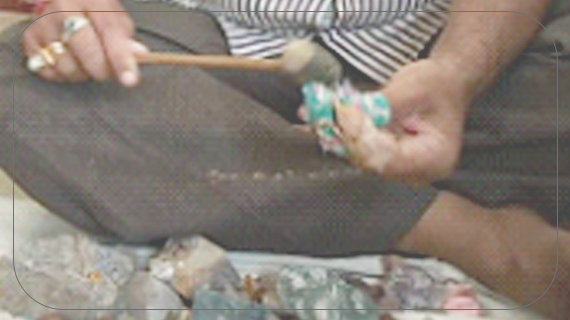
Chipping
A pointy iron rod is implanted in the ground at a certain angle. A stone is than held against the rod by hand and is struck with a hammer made of animal horn example cow’s horn, so that the stone is chipped into small pieces. The chipper must break the stone while keeping in mind the final product which is to be created hence this job requires skills for work.
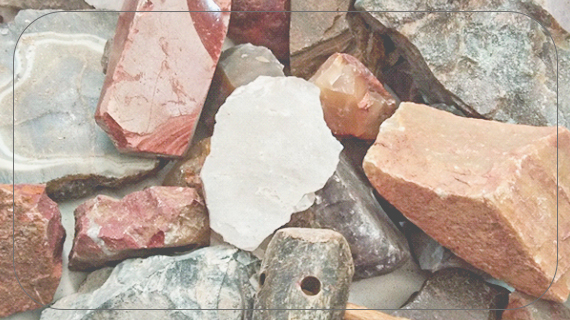
Secondary Heating
Some beads require seven to ten firings before they achieve the deep red color representative of the highest quality of carnelian. Improper heating can result in wasted fuel and/or cracked beads. Invariably some of the bead roughouts or finished beads do become cracked or spalled, and many of these are lost in the ashes of the kiln.
Through the examination of kiln waste it is possible to reconstruct the general scale of production, the quality of the raw materials being processed, and the varieties of finished objects being produced.

Grinding
Before the introduction of electrically powered emery wheels the bead roughout was ground and shaped on a hard sandstone or quartzite grinding stone. Different shapes of grinding stones must be used to shape different varieties of beads and they would provide an important archaeological indicator for bead grinding. The dust from bead grinding would also be an important indicator, as long as it was not removed for use as an abrasive in sawing or polishing. Very few ground beads would be lost through hand- grinding techniques, though there would be some breakage due to improper pressure or flaws in the bead roughout.
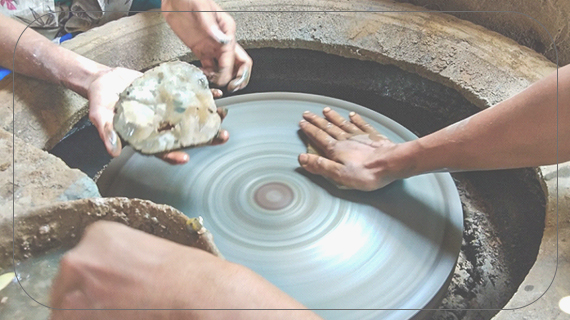
Rounding
Rounding and process of reduction of the size is sometimes done in a drum made of wooden planks – a sort of a barrel of ball mill, powered through an electric motor. The process is very dusty and noisy. Many people especially the men of the working class who employees other workers, but many also work alongside the workers to build walls around the mill to prevent silica dust from spreading everywhere in the work environment. The walls also help to reduce the noise pollution created by the ball mill machine.
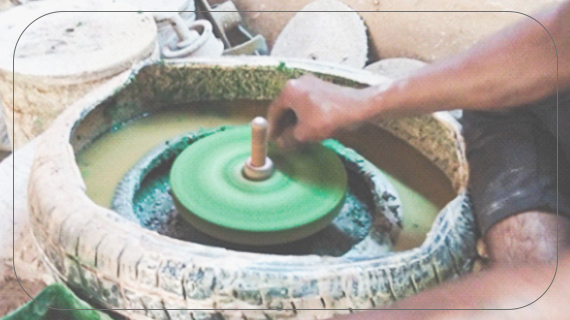
Polishing
Polishing or Grinding is done by polishers or grinders. These people are the most vulnerable to exposure of silica dust. Polishing is done in various ways depending on the final product. For creation of certain products, a horizontal wooden bench with a vertical moving emery wheel powered by an electric motor is commonly used. Polishing done by hand is done dry, though many workers have started to adapt wet methods for polishing the stone. For shaping spherical beads, polishers use a wooden plank of about 6-8 inches wide and 2 – 3 feet long.